DGFox 60 Evo
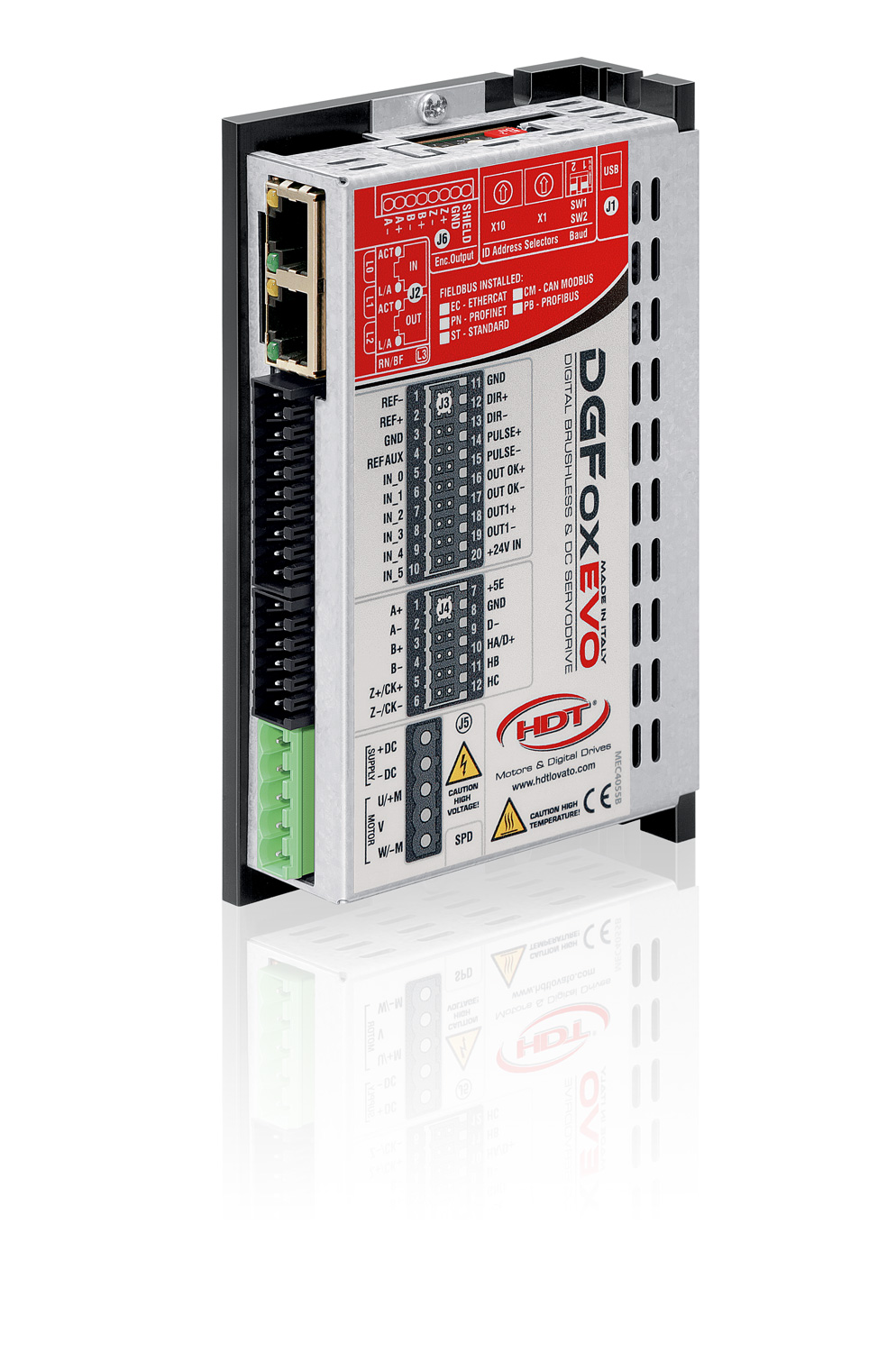
Description
DGFox60 Evo® by HDT is a sinusoidal digital digital servo drive in single-axis execution for operation from low voltage DC power supply, from 20 to 80VDC. Current sizes up to 13A corresponding to nominal powers up to 900W.
DGFox60 Evo® allows the motor control of rotary and linear brushless servomotors, and in direct current with permanent magnets equipped with encoder.
Control both from analog reference, Pulse/Dir and from EtherCat, ProfiNet, CanOpen and Modbus protocol.
Feedback from incremental encoders, SSI absolute encoders.
DGFox60 Evo® integrates speed, torque, positioner, electric axis, electronic cam and pressure control as standard.
Easy to program, they connect via the USB port to the fast Caliper management software
Main Features.
Control method |
||
Digital regulation loop for torque, speed and position. |
- for AC brushless synchronous motor, rotary and linear: FOC control, SVM modulation, with feedback or sensorless. |
|
Main reference |
||
Analog |
±10V differential speed and torque 12Bit |
|
Auxiliary reference |
||
Analog |
0/+10V single ended - 12Bit |
|
Frequency reference |
||
Speed and position |
- Pulses and direction ( 2MHz ) |
|
Optional fiedlbuses |
||
- Modbus RTU |
||
Main feedback |
||
Hall's sensor |
- with sequence at 120° angle |
|
Encoder 5V |
- Incremental 5V Line Drive with/without Hall sensors |
|
Encoder output |
||
Repetition |
- ABZ channels repetition of the main feedback |
|
Control Mode |
||
Speed |
- Speed with/without torque limits. Adjustable trapezoidal or "S" ramps. |
|
Torque |
- Torque control |
|
Position |
- Multi-positioner: Single target, from cyclic/acyclic table, from analog input. |
|
Configurable inputs and outputs |
||
Input |
- 6 digital inputs NPN/PNP (2 Touch Probe) |
|
Output |
- 2 digital output NPN/PNP |
|
Digital filters |
||
- Observer on motor feedback. |
||
Drive and motor protection functions |
||
- Shortcircuit |
||
Drive interface |
||
- 3 LEDs on the drive for signaling status and alarms. Complete information via fieldbus. |
||
Braking management |
||
- Braking in torque limit in case of Limit Switch in mechanical stop |
||
Drive parametrization |
||
- Via CALIPER 4.0 software through the micro USB 2.0 port |
||
Additional features |
||
- Motor autophasing procedure available for every type of feedback. |
Taglie in corrente
Sizes | U.m. | 2.5 | 5 | 8 |
10 | 13 |
Voltage supply | VDC | 60VDC |
||||
Min/Max voltage supply | VDC | 20÷80 VDC |
||||
Rated current | Arms | 2.5 | 5 | 8 |
10 | 13 |
Peak current for 2” | Arms | 5 | 10 | 16 |
20 | 26 |
Rated output power | KW | 0.175 | 0,35 | 0,55 |
0,70 |
0,90 |
Logic power supply | VDC | 24VDC ± 20% | ||||
Internal braking resistor |
NO | |||||
Dimensions | T0 | |||||
Weight | Kg | 0,39 |
Dimensions
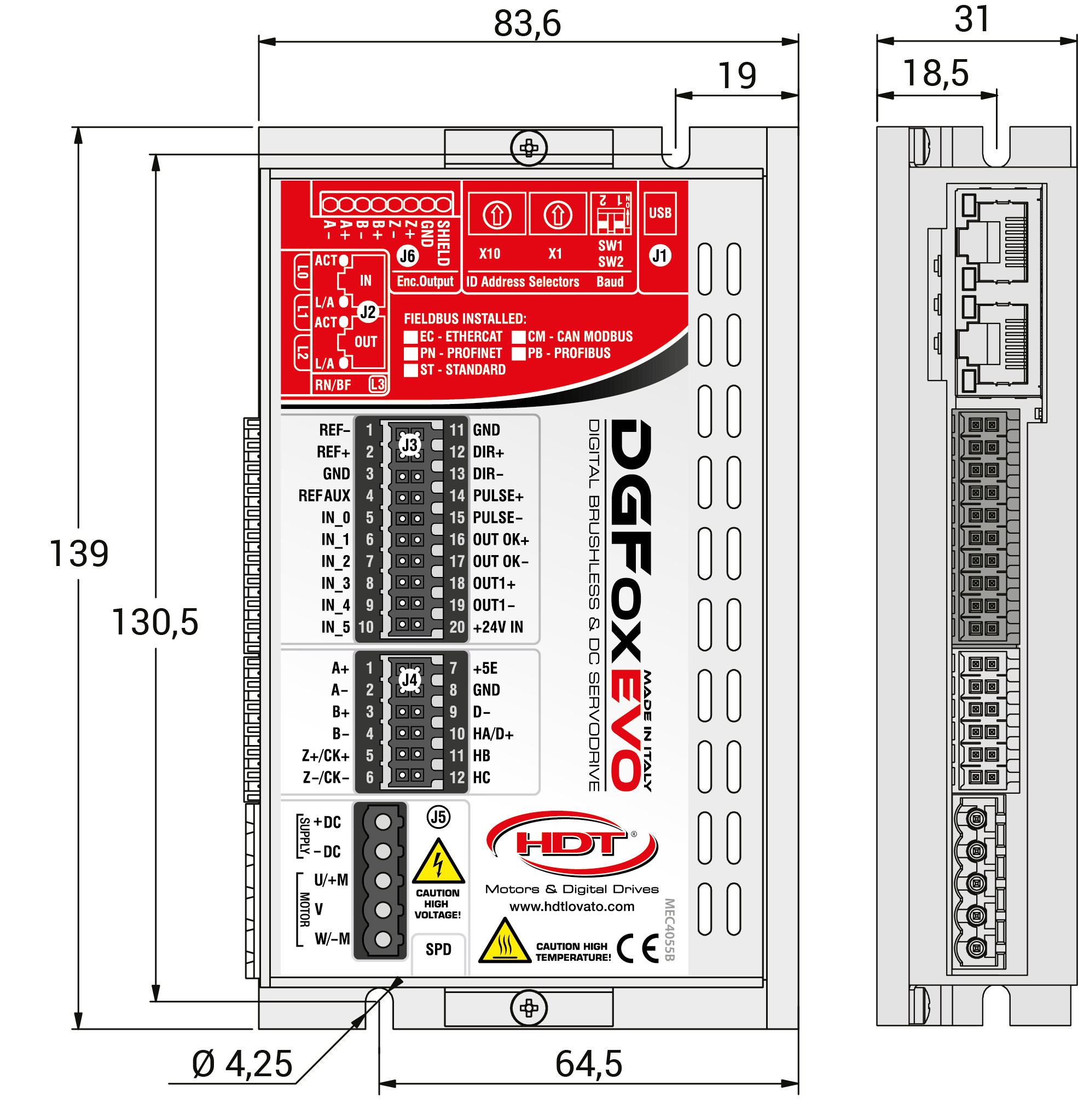