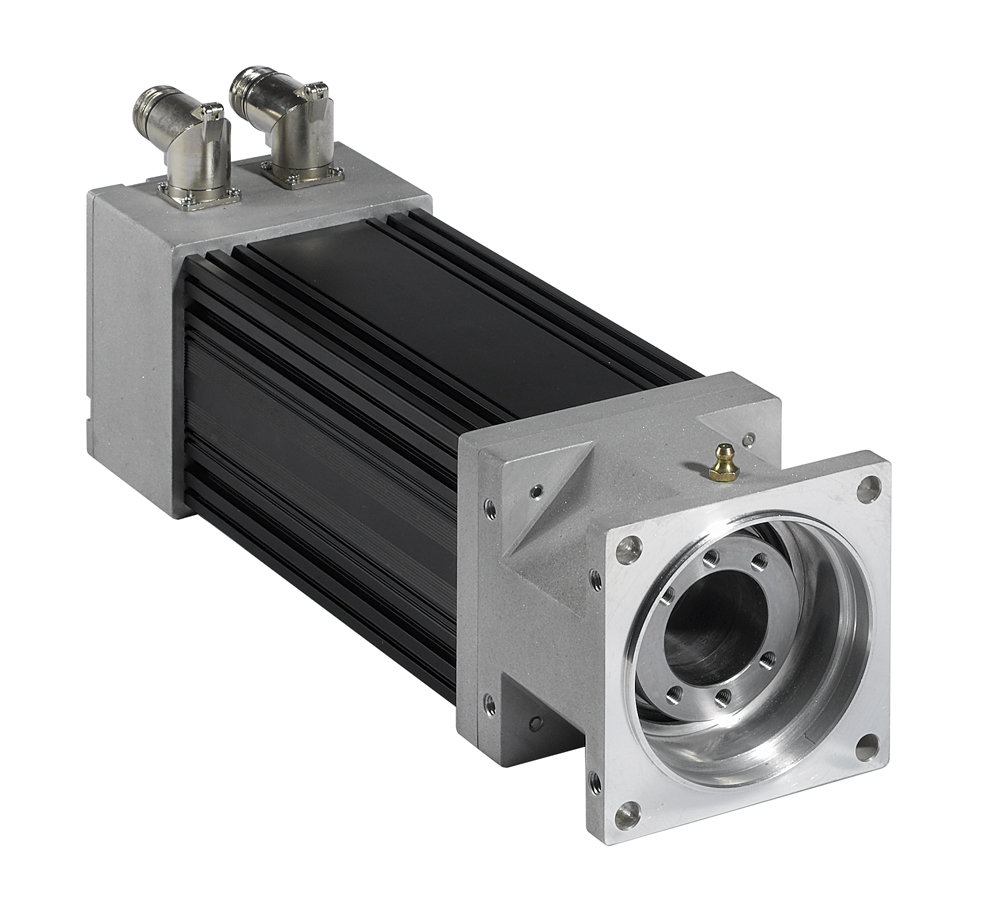
BSP10 Linear servoactuator
Brushless servoactuators, natural air cooling.
Version with through hole for nut for 25mm screw.
Mechanics with flange in 110mm square case.
Torque in service S1 of 9Nm.
Nominal speed of 3000rpm.
Winding for 400VAC network.
Electrical Data ( voltage 400VAC )
Max speed with screw of 10mm lead*
Version for 400VAC power supply a 400VAC |
Symbol | U.mis. | BSP10G |
Drive power supply voltage |
400VAC | ||
Stall torque at 100K Dt |
To | Nm | 9.05 |
Theoretical force with screw 5mm lead | Fo | N | 11300 |
Theoretical force with screw 10mm lead | Fo | N5600 | 5600 |
Rated speed | n | RPM | 3000 |
Max speed with screw of 5mm lead* | v | mm/sec | 250 |
Max speed with screw of 10mm lead* | v | mm/sec | 500 |
Power at rated speed 100K Dt | Pn | W |
2910 |
Torque at rated speed 100K Dt | Tn |
Nm |
3 |
Peak torque | Tpk |
Nm |
24.44 |
Poles number | PN | 6 | |
Winding resistance 20°C phase/phase | Rw |
Ohm |
2.25 |
Inductance phase/phase 50Hz | Lw |
mH | 10.90 |
EMF constant ref. at 20°C | Ke | Vs | 0.92 |
Torque constant | Kt | Nm/Arms | 1.59 |
Torque constant at 100°C | Vn | V |
320 |
Current of stall at 100K Dt | Io |
A | 5.7 |
Current at rated speed at 100K Dt | In |
A | 5.9 |
Peak current | Ipk | A | 15.35 |
Demagnetization current | Idm |
A | 41.80 |
* screw/nut system not supplied with the motor and not suppliable by HDT. |
Mechanical Data
Motor type BSP10 |
Symbol | U.mis. | BSP10G | ||
Screw/nut diameter according to standard DIN69051 | Ø | mm | 25 | ||
Rotor inertia | Jm | mKgm2 | 1.164289 | ||
Rotor inertia ( motor with brake) | Jmb | mKgm2 |
1.262283 | ||
Weight | M | Kg |
13.7 | ||
Weight with brake |
Mb | kg |
14.6 |
Thermal features
Motor type BSP10 |
Symbol | U.mis. | BSP07M | BSP07G | ||
Operating temperature | °C | 0÷40 | ||||
Insulation class | Winding class H - Motor class F | |||||
Cooling system | Natural Air: IC0041 | |||||
Standard protection |
IP65 ( shaft excluded ) |
Brake specs
Brake parameters |
Symbol | U.mis. | BSP07G | |
Brake type | 06 | |||
Static brake torque at 100°C* | Tb | Nm | 9 | |
Brake power at 20°C | Pb | W | 18.0 | |
Coupling time | ms | 2 | ||
Release time | ms | 40 | ||
Voltage ±5% | VDC | 24 | ||
Backlash | Arcmin | 0 | ||
*torque obtained after running in |
Standard technical specifications
Type |
||
- low inertia permanent magnet servomotor |
||
Rotore |
||
- rare earth permanent magnets ( NdFeB ) |
||
Insulation |
||
- winding, class H; Motor Class F |
||
Winding |
||
Standard |
- 3000rpm |
|
On demand |
- other combinations of voltage and speed possible. |
|
Insulation |
- winding in class H |
|
Thermal protection sensors |
||
Standard |
- PTC |
|
Optional |
- No options |
|
Cooling system |
||
|
- Natural air ( IC0041 ) |
|
Standard protection |
||
- IP50 (exclusion of the shaft side). |
||
Ballbearing |
||
-ball bearings with double screen lubricated for life. 20,000 operating hours under normal conditions of use . |
||
Balancing |
||
- Grade "R" |
||
Concentricity and perpendicularity of the axis/flange |
||
- grade "N" (normal) - acording to IEC 72 - DIN0530 |
||
Shaft output |
||
-with 40mm diameter through hole prepared for nut housing for 25mm screw type DIN69051 |
||
Brake |
||
- optional. Permanent magnet parking brake, 24VDC power supply with specific polarity. Brake engaged in the absence of power supply. Braking torque greater than the motor Tn |
||
Connections and cables |
||
Power |
- with angular connector type M23 shaft side ( code G ) |
|
Signal |
- with angular connector type M23 shaft side ( code G ) |
|
Position transducer |
||
- Resolver |
Dimensions
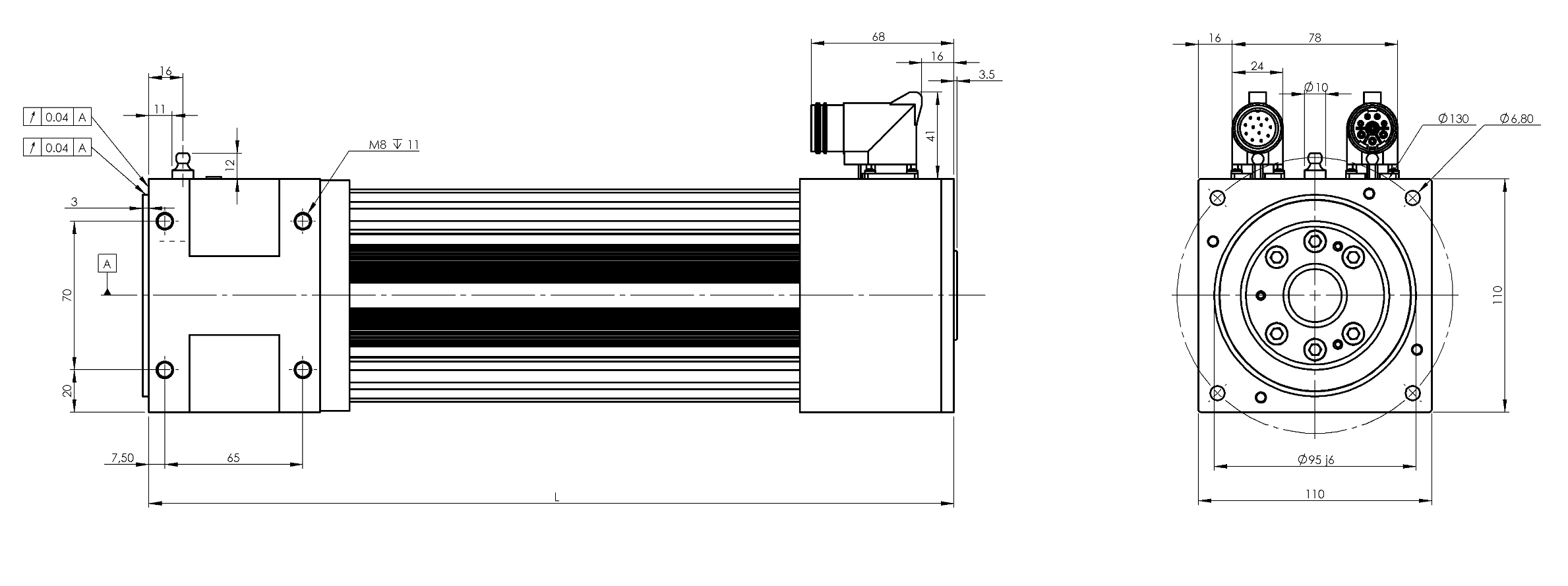
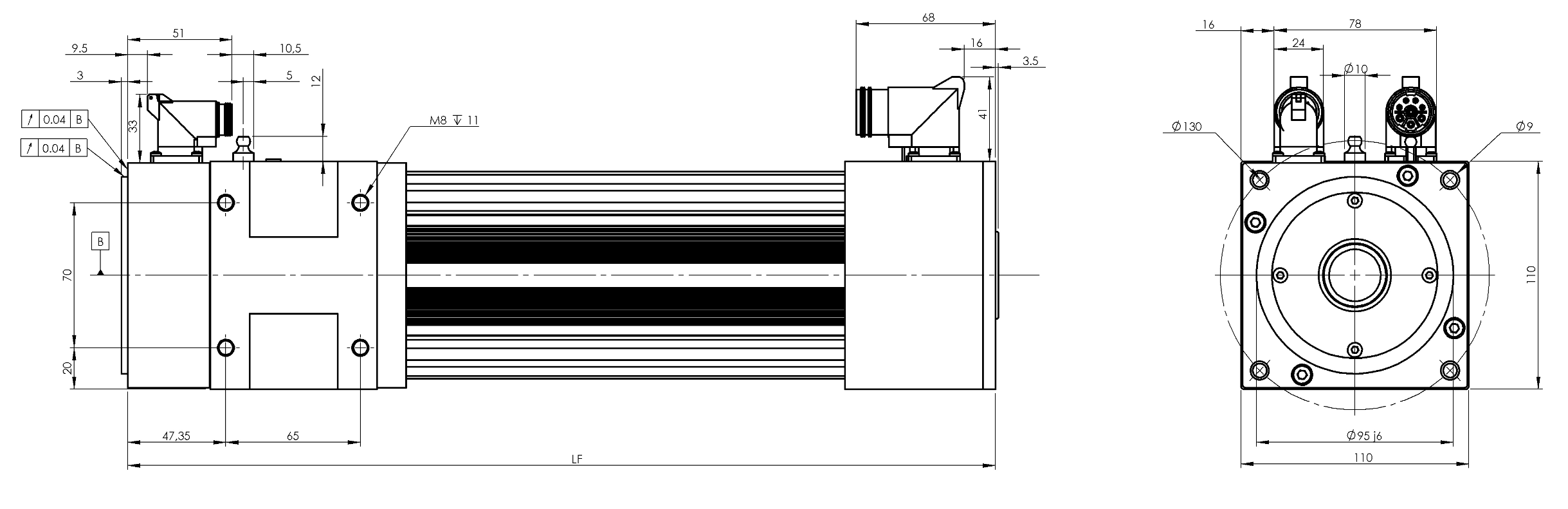
Motor type |
L | LF | Note |
BSP10G |
379 | 418.5 |