NTT240
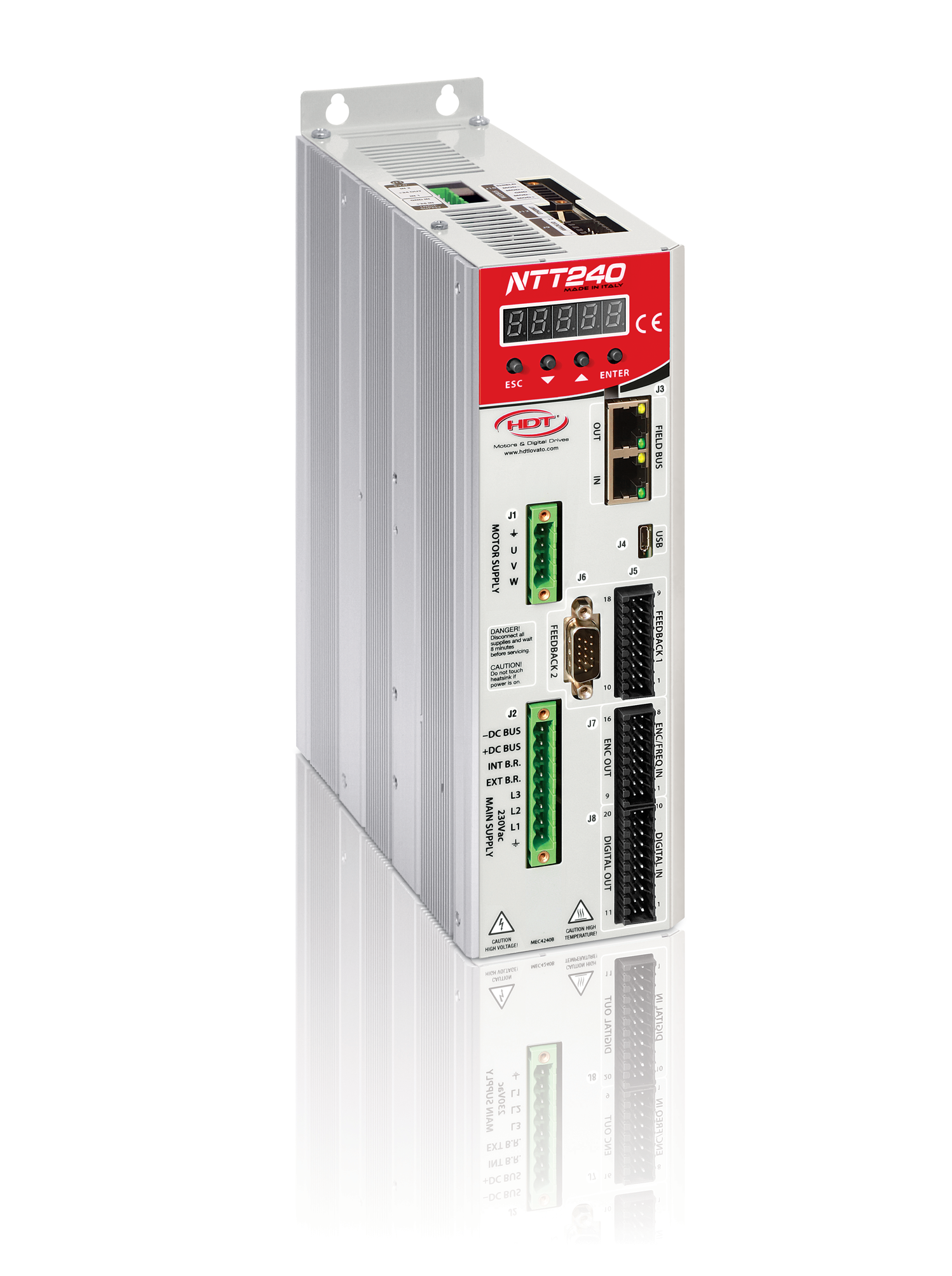
Description
The HDT NTT240® series includes a complete range of digital single-axis servodrives for operation on 230VAC networks with current sizes up to 10A corresponding to nominal powers up to 3kW.
NTT240® allows the motor control of brushless, asynchronous servomotors, in direct current with permanent and linear magnets.
Piloting both from the analog reference and from the EtherCat, ProfiNet, CanOpen and Modbus protocols.
Feedback from incremental encoders, absolute and resolver encoders.
NTT240® integrates as standard the speed, torque, positioner, electric axis, electronic cam and pressure control.
An Ethernet port allows connection to the network and even the remote monitoring*.
Easy to program, they connect via the USB port to the fast Caliper management software.
Main Features
Control method |
||
Digital regulation, loop for torque, speed and position. |
- for AC brushless synchronous motor,rotary and linear: FOC control, SVM modulation, with feedback or sensorless. |
|
Main reference |
||
Analog |
± 10V differential speed and torque 16Bit |
|
Reference auxiliary |
||
Analog |
±10V differential speed, torque and position 12Bit |
|
Frequency reference |
||
Speed and position |
- Pulses and direction ( 2MHz ) |
|
Optional fieldbuses |
||
- Modbus RTU |
||
Main feedback |
||
Hall's sensor |
-120° sequence; |
|
Encoder |
- Incremental 5V Line Drive with/without Hall sensors (adjustale power supply form 5 to 9V) |
|
Sensorless |
- Sernsorless FOC and V/Hz |
|
Second optional feedback |
||
Resolver |
- 16 Bit with simulated encoder 5V Line Drives. |
|
Encoder |
- Hyperface + SinCos |
|
Encoder output |
||
Simulated encoder |
- for resolver feedback: possibility to select 256, 1024, 4096 o 16384ppr |
|
Repetition |
- ABZ channels repetiotion of the main feedback |
|
Control mode |
||
Speed |
- Speed with/withou torque limit. - Adjustable trapezoidal or "S" ramps. |
|
Torque |
- Torque control |
|
Position |
- Multi-positioner: Single target, from cyclic/acyclic table, analog |
|
Pressure |
- Pressure control |
|
Configurable inputs and outputs |
||
Input |
- 8 digital inputs PNP ( 2 Touch Probe ) |
|
Output |
- 6 digital outputs PNP |
|
Digital filters |
||
- Observer on motor feedback. |
||
Drive and motor protection function |
||
- Shortcircuit |
||
Drive interface |
||
- 5 digits display and keys for displaying and managing the status of the drive and its parameters |
||
Safety function |
||
- STO Safe Torque Off: IEC61800-5 - SIL3 Cat.0: EN61508 |
||
Braking management |
||
- Integrated brake management with immediate or ramp stop |
||
Drive parametrization |
||
- Via CALIPER 4.0 software through the microUSB port |
||
Additional features |
||
- Motor autophasing procedure available for every type of feedback. |
The HDT NTT460® series includes a complete range of digital single-axis servo drives for operation on 400VAC networks with current sizes up to 75A corresponding to nominal powers up to 40kW.
NTT460® allows the motor control of brushless, asynchronous servomotors, in direct current with permanent and linear magnets.
Piloting both from the analog reference and from the EtherCat, ProfiNet, CanOpen and Modbus protocol.
Feedback from incremental encoders, absolute and resolver encoders.
NTT460® integrates as standard the speed, torque, positioner, electric axis, electronic cam and pressure control.
An Ethernet port allows connection to the corporate network and even remote monitoring.
Easy to program, they connect via the USB port to the fast Caliper management softwareCurrent Sizes
Sizes | U.m. | 1.5 | 3 | 6 | 10 |
Power supply | VAC | 230VAC 1PH - 3Ph |
|||
Min/Max supply voltage | VDC | 230VAC ±15% - 50/60Hz |
|||
DC Min/Max supply voltage | VDC | 200 VDC ÷ 360 VDC |
|||
Rated current | Arms | 1.5 | 3 | 6 | 10 |
Current peak for 2” | Arms | 3 | 6 | 12 | 20 |
Rated output power | KW | 0.5 | 1 | 1.5 | 3 |
Internal braking resistor | W | NO | NO | SI | SI |
External optional braking resistor output | SI | ||||
EMC Internal Filter | SI | ||||
Logic supply | VDC | 24VDC ± 20% | |||
Dynamic forced ventilation | NO | SI | |||
Dimensiont | T0 | T1 |
T2 | ||
Weight | Kg | 2 |
2.4 | 26 |
|
Safety functions | STO - Safe Torque Off: IEC61800-5-2:2007 - SIL3 Cat.0: EN61508:2001 ( EN954-1:1996 ) | ||||
*= ( EMC 61800-3 cat.C3) |
Dimensions
Taglie drive (mm) | T0 | T1 | T2 |
A | 67,2 | 83 | 103 |
A1 | 33,7 | 47,7 | 67,6 |
A2 | - | 40 | 40 |
B | 216,5 | ||
B1 | 231,5 | ||
B2 | 241,5 | ||
C | 173,5 | 188,5 | |
C1 | 60 | ||
D | ∅4,5 |
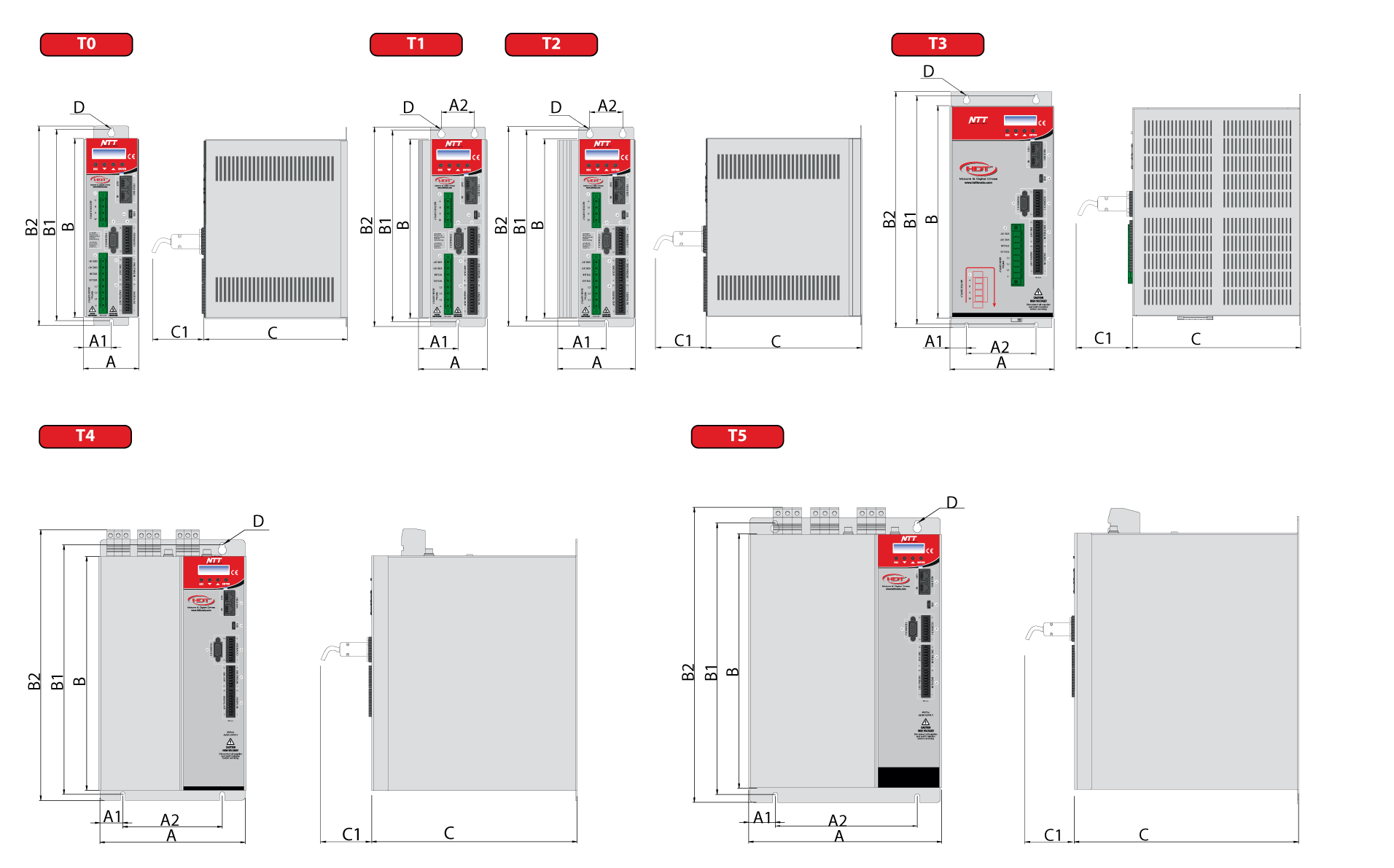